In today’s rapidly evolving technological landscape, artificial intelligence (AI) is revolutionizing various industries, and engineering is no exception. With its ability to process vast amounts of data, identify patterns, and make informed decisions, AI is transforming traditional engineering practices, enabling engineers to tackle complex challenges more efficiently and effectively than ever before.
The foremost advantage of AI lies in its ability to simplify tasks, primarily through automation. By employing finely tuned algorithms, AI can manage mundane and predictable responsibilities, allowing engineers to allocate their time more effectively towards substantial endeavors. However, there exist limitations to this automation. For it to be dependable, tasks must adhere to patterns and possess minimal variation thresholds. Analogous to automated processes in grocery stores handling inventory, AI excels in scenarios with clear-cut outcomes – an item either exists on the shelf or it doesn’t.
In the engineering realm, AI proves invaluable yet encounters analogous constraints. Despite its capabilities, AI cannot fully replicate the creative thought processes inherent to human engineers. Nevertheless, AI contributes by generating novel designs and conducting simulations to forecast performance outcomes. These simulations offer significant advantages to working engineers, expediting scenario testing with enhanced accuracy, thereby revolutionizing traditional engineering practices.
Introduction to AI in Engineering
The integration of AI in engineering encompasses a wide range of applications, from design and optimization to maintenance and decision-making. By leveraging AI algorithms and techniques such as machine learning, neural networks, and natural language processing, engineers can automate tasks, predict outcomes, and optimize processes across various engineering disciplines.
As the evolution of AI continues, its impact on engineering processes and methodologies is poised to be profound. Many tedious and repetitive tasks stand to be supplanted by AI workflows, owing to its unparalleled speed in generating results. However, it remains crucial to scrutinize, verify, and enhance the data produced by AI systems. Consequently, I perceive AI not as a threat to engineers at present.
Engineers must adapt to this evolving landscape to avoid lagging behind peers and competitors. Emphasizing continuous learning and experimentation with AI-based tools will be pivotal to ensure the workforce remains abreast of the latest advancements. When wielded judiciously, AI holds the potential to significantly enhance the efficacy of engineers.
Furthermore, AI’s influence on the engineering domain extends beyond direct applications. Despite nearly three years since the onset of the pandemic, design engineers continue to grapple with supply chain instability. AI plays a crucial role in mitigating such challenges by streamlining network management and offering accurate forecasts for potential disruptions like adverse weather conditions or viral outbreaks, enabling proactive adjustments to routes.
Additionally, AI finds utility in optimizing goods transportation. IoT sensors installed on long-haul trucks monitor vehicle conditions and provide detailed route recommendations, thereby boosting productivity.
While the advancement of AI may prompt speculation about the future role of engineers, it’s challenging to envision a world devoid of their expertise in the near term. Long-term studies suggest that technological progress tends to create more job opportunities than it eliminates. Engineers, with their STEM-driven acumen, are well-equipped to thrive in the evolving work landscape shaped by AI.
Design and Optimization
AI-powered design tools are revolutionizing the engineering design process, allowing engineers to generate innovative solutions and optimize designs faster than ever before. Through generative design algorithms, AI can explore vast design spaces, generate numerous design alternatives, and identify optimal solutions based on specified criteria. This not only accelerates the design process but also enables engineers to explore design possibilities that may have been overlooked using traditional methods.
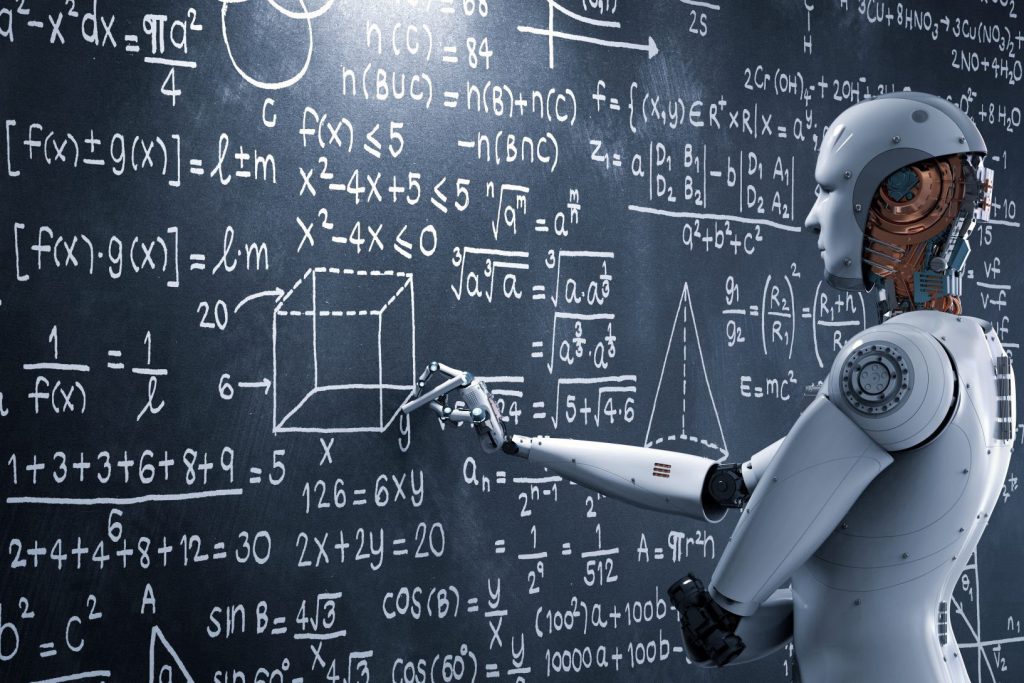
Predictive Maintenance
Predictive maintenance is revolutionizing the way industries approach equipment maintenance, leveraging the power of artificial intelligence (AI) to predict and prevent potential failures before they occur. By harnessing AI algorithms and advanced analytics, predictive maintenance enables organizations to optimize maintenance schedules, minimize downtime, and extend the lifespan of critical assets.
Predictive maintenance is a proactive approach to maintenance that uses data analytics, machine learning, and sensor technology to predict equipment failures and schedule maintenance tasks accordingly. Unlike traditional reactive or scheduled maintenance methods, which can be costly and inefficient, predictive maintenance allows organizations to address maintenance needs precisely when they arise, optimizing resources and maximizing equipment uptime.
Predictive maintenance relies on several key components to effectively predict and prevent equipment failures:
- Data Acquisition: Predictive maintenance begins with the collection of data from sensors, IoT devices, and other sources, capturing information about equipment performance, operating conditions, and environmental factors.
- Data Preprocessing: Once collected, the raw data is preprocessed to remove noise, normalize values, and prepare it for analysis. This preprocessing step is crucial for ensuring the accuracy and reliability of predictive maintenance models.
- Feature Engineering: Feature engineering involves selecting and transforming relevant data attributes (features) that are predictive of equipment failure. This step plays a critical role in building accurate predictive maintenance models.
- Model Development: Predictive maintenance models are built using machine learning algorithms, such as regression, decision trees, or neural networks. These models analyze historical data to identify patterns and trends indicative of potential equipment failures.
- Model Training and Validation: Predictive maintenance models are trained using historical data and validated using unseen data to ensure their accuracy and reliability in predicting equipment failures.
- Predictive Analytics: Once deployed, predictive maintenance models continuously analyze real-time data to identify early warning signs of equipment degradation or failure, triggering maintenance alerts or recommendations.
Smart Manufacturing
Smart manufacturing represents a paradigm shift in the industrial landscape, leveraging advanced technologies such as artificial intelligence (AI), the Internet of Things (IoT), and automation to optimize manufacturing processes, improve efficiency, and drive innovation.
Smart manufacturing, also known as Industry 4.0 or the Fourth Industrial Revolution, is characterized by the integration of digital technologies into manufacturing processes to create intelligent, interconnected systems. By connecting machines, sensors, and devices across the production line, smart manufacturing enables real-time data collection, analysis, and decision-making, leading to more agile, responsive, and efficient manufacturing operations.
Smart manufacturing encompasses several key components, including:
- Internet of Things (IoT): IoT devices, such as sensors and actuators, are embedded into manufacturing equipment to collect and transmit data in real-time, enabling remote monitoring, predictive maintenance, and process optimization.
- Artificial Intelligence (AI): AI algorithms analyze vast amounts of data collected from IoT devices to identify patterns, trends, and anomalies, enabling predictive analytics, optimization, and automation of manufacturing processes.
- Big Data Analytics: Big data analytics techniques are used to process and analyze large volumes of structured and unstructured data generated by manufacturing systems, enabling actionable insights and informed decision-making.
- Cloud Computing: Cloud computing platforms provide scalable and flexible infrastructure for storing, processing, and sharing manufacturing data and applications, enabling collaboration, accessibility, and scalability.
- Cyber-Physical Systems: Cyber-physical systems integrate physical components with digital technologies to create interconnected systems that monitor, control, and optimize manufacturing processes in real-time.
Benefits of Smart Manufacturing
- Improved Efficiency: By optimizing production processes and reducing downtime, smart manufacturing improves overall efficiency, productivity, and throughput.
- Cost Reduction: Smart manufacturing enables cost savings through reduced waste, improved resource utilization, and predictive maintenance, resulting in lower operational costs and higher profitability.
- Quality Enhancement: By monitoring and controlling manufacturing processes in real-time, smart manufacturing improves product quality, consistency, and compliance with quality standards.
- Agility and Flexibility: Smart manufacturing systems are more agile and adaptable to changes in demand, market conditions, and production requirements, enabling faster response times and greater flexibility.
- Innovation and Competitiveness: Smart manufacturing fosters innovation by enabling the development of new products, processes, and business models, enhancing competitiveness and driving growth in the global marketplace.
Challenges and Considerations
Despite its numerous benefits, smart manufacturing also presents challenges and considerations, including:
- Data Security and Privacy: Smart manufacturing involves the collection, transmission, and storage of sensitive manufacturing data, raising concerns about data security, privacy, and protection against cyber threats.
- Skill Gaps and Workforce Training: The implementation of smart manufacturing requires a skilled workforce capable of operating and maintaining advanced technologies. Addressing skill gaps and providing workforce training is essential for successful adoption and integration of smart manufacturing solutions.
- Interoperability and Standardization: Integrating disparate manufacturing systems and technologies can be challenging due to interoperability issues and lack of industry standards. Standardization efforts are needed to ensure compatibility, interoperability, and seamless integration of smart manufacturing solutions.
- Investment and ROI: The upfront costs associated with implementing smart manufacturing solutions, such as IoT devices, AI algorithms, and cyber-physical systems, can be significant. Demonstrating a return on investment (ROI) and quantifying the benefits of smart manufacturing is essential for securing buy-in from stakeholders and decision-makers.
Autonomous Systems
Autonomous systems, propelled by artificial intelligence (AI), represent a transformative leap in engineering capabilities. These systems are designed to operate independently with minimal human intervention, relying on advanced algorithms to perceive and interpret their surroundings, make decisions, and execute tasks. In sectors like transportation, autonomous vehicles are revolutionizing mobility by navigating roads and highways without human drivers, while UAVs are being deployed for tasks such as aerial surveillance and package delivery. Moreover, in fields like agriculture, autonomous drones equipped with sensors and AI algorithms can monitor crop health, optimize irrigation, and even perform precision spraying, enhancing productivity and sustainability.
The integration of AI into autonomous systems has far-reaching implications across various engineering domains. By automating routine tasks and enabling machines to adapt to dynamic environments, these systems improve operational efficiency, reduce human error, and enhance safety. Furthermore, they open up new avenues for innovation and exploration, allowing engineers to tackle challenges in fields such as infrastructure inspection, disaster response, and environmental monitoring with greater precision and effectiveness. As AI technology continues to evolve, autonomous systems will play an increasingly integral role in reshaping industries and driving progress in engineering towards a future of smarter, more interconnected, and autonomous operations.
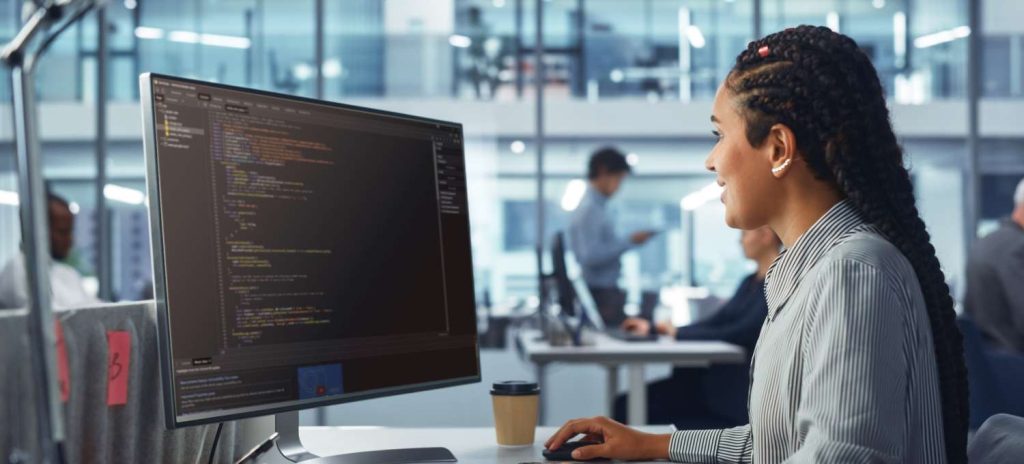
Challenges and Considerations
The integration of AI in engineering undoubtedly brings about a multitude of advantages, yet it also introduces a set of challenges and considerations that necessitate careful attention. One prominent concern is the issue of data privacy and security. With AI systems relying heavily on vast amounts of data, ensuring the protection and confidentiality of sensitive information becomes paramount. Additionally, the ethical implications of AI-driven decision-making raise significant questions. As machines become more autonomous in their decision-making processes, ethical frameworks must be established to govern their behavior and ensure alignment with societal values and norms.
Furthermore, the responsible development and deployment of AI technologies in engineering require interdisciplinary collaboration. Engineers must work closely with experts in fields such as ethics, law, and social sciences to address the broader implications of AI integration. This collaboration is essential for developing AI systems that not only perform effectively but also uphold ethical standards and respect human rights. By addressing these challenges and considerations, the integration of AI in engineering can proceed in a manner that maximizes its benefits while mitigating potential risks and ensuring its ethical and responsible use.
Another critical challenge in integrating AI into engineering is the potential for biases and discrimination within AI algorithms. If not properly addressed, these biases can lead to unfair outcomes and perpetuate existing social inequalities. Engineers must actively work to identify and mitigate biases in AI models, ensuring fairness and equity in their applications. Additionally, the rapid advancement of AI technology often outpaces the development of regulations and standards, creating a legal and regulatory landscape that is still evolving. This dynamic environment presents challenges in terms of ensuring compliance with existing laws and regulations while also adapting to emerging ethical and legal considerations surrounding AI.
Moreover, the complexity and opacity of AI algorithms pose challenges in terms of understanding and explaining their decision-making processes. Engineers face the task of making AI systems transparent and interpretable, allowing stakeholders to understand how decisions are made and hold AI systems accountable for their actions. Finally, there is a growing concern about the potential impact of AI on employment and the workforce. While AI has the potential to automate routine tasks and improve productivity, it also raises questions about job displacement and the need for reskilling and retraining programs to ensure a smooth transition for workers in industries affected by AI adoption. Addressing these challenges requires a concerted effort from engineers, policymakers, and stakeholders to navigate the complex ethical, legal, and societal implications of AI in engineering.
Future Directions
Looking ahead, the future of AI in engineering holds immense potential for further innovation and transformation. Advancements in AI research, coupled with the continued integration of AI into engineering practices, will enable engineers to tackle increasingly complex challenges and unlock new opportunities for growth and advancement across various industries.
In conclusion, the integration of AI in engineering is revolutionizing how engineers design, optimize, and operate systems and processes. From design and optimization to predictive maintenance, smart manufacturing, and autonomous systems, AI is driving innovation and reshaping the future of engineering. By embracing AI technologies and leveraging their capabilities, engineers can unlock new levels of efficiency, productivity, and sustainability in the pursuit of engineering excellence.
Conclusion
In conclusion, the integration of AI in engineering represents a transformative shift in how tasks are approached and executed across various domains. From design and optimization to predictive maintenance, smart manufacturing, and autonomous systems, AI is revolutionizing traditional engineering practices and opening up new possibilities for innovation and advancement. While the benefits of AI in engineering are abundant, it is crucial to address challenges such as data privacy, biases in algorithms, and the evolving regulatory landscape.
Despite these challenges, the future of AI in engineering holds immense promise. Advancements in AI research and interdisciplinary collaboration will continue to drive innovation, enabling engineers to tackle increasingly complex challenges and unlock new opportunities for growth and advancement. By embracing AI technologies and leveraging their capabilities responsibly, engineers can pave the way for a future of smarter, more efficient, and sustainable engineering solutions. As AI continues to evolve, it will undoubtedly play a pivotal role in shaping the future of engineering and driving progress towards a more interconnected and autonomous world.